Vacuum Pump and Compressor, A vacuum pump is a device that extracts gases and air from a closed space, resulting in the illusion of a low-pressure or vacuum. It is employed in many applications, ranging from studies to packaging food items.
Compressors are instruments that can increase air or gas pressure by decreasing the volume. It plays an important role in various industries, including manufacturing transport, refrigeration, and other industries to ensure efficiency in processes and control the temperature.
What is a Vacuum Pump?
Vacuum pumps are devices created to remove gases or air from a container that is sealed and create a vacuum or a low-pressure environment inside the container.
The process is generally known as “vacuum pumping” or “evacuation.” Vacuum pumps are employed for a myriad of industries, such as:
- Scientific as well as Laboratory work: Vacuum pumps are vital in labs for tasks like degassing samples, distillation, freeze-drying, and creating controlled conditions for testing.
- Manufacturing as well as Industrial processes: Industries like semiconductor manufacturing, chemical processing, and food packaging depend on vacuum pumps to eliminate the gases and air from the processing chambers and packaging materials.
- Medical and Health: Vacuum pumps can be found in medical devices such as suction machines. They create a vacuum to facilitate procedures like wound drainage, dental suction, as well as blood collection.
- Automotive: repair and maintenance vacuum pumps may be utilized for jobs such as bleeding brakes and A/C system elimination and evaluating components that operate with a vacuum.
- Environmental Monitoring: Vacuum pumps can be found in equipment for environmental monitoring to take air samples to analyze for determining the levels of pollution or identifying airborne pollutants.
- HVAC systems: Vacuum pumps are employed during the installation and repair of heating ventilators as well as air conditioning (HVAC) systems to remove humidity and air from refrigerant lines.
- Aerospace: For aerospace-related applications vacuum pumps are utilized to simulate the space vacuum for testing purposes, and also to extract air from satellite propulsion systems.
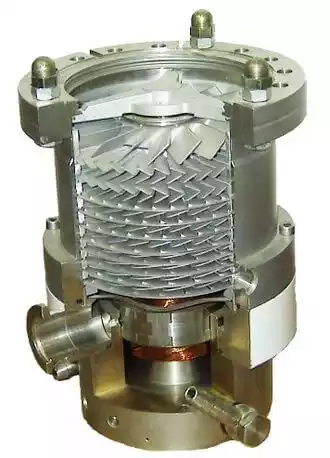
There are many types of vacuum pumps. Each has distinct working principles and is suitable for particular uses. The most common kinds of vacuum pumps are:
- The Rotary Vane Pump: It uses vanes that rotate to create vacuums by the trapping and compression of gas molecules.
- Diaphragm Pump: Diaphragm pumps utilize diaphragms with flexible diaphragms for creating a vacuum expansion and contraction of the space inside the chamber of the pump.
- Scroll Pump: Scroll pumps employ two spiral scrolls interlocking to compress and hold gas molecules, forming an air vacuum.
- Turbomolecular Pump: Turbomolecular pumps can be used for the creation of ultra-high vacuums. They are used in both semiconductor and scientific applications.
- Venturi Pump: The Venturi pump operates by generating a pressure differential through an encircled tube which pulls gas molecules from the container.
The selection of a vacuum pump is based on various aspects like the needed level of vacuum, the amount of gas that needs to be evacuated, and the particular application’s needs. Vacuum pumps play a crucial part in many industries by making it possible to conduct experiments and processes that require controlled conditions of vacuum.
What is a Compressor?
The compressor can be described as a device that increases the pressure of gases or diminutes the volume. It is an essential element in a myriad of industries and is used for the purpose of compressing gases to serve different purposes.
Compressors are typically used in industries as well as HVAC (heating, ventilation as well and air conditioning) systems along with refrigeration, as well as many other areas. The main role of a compressor is to draw in low-pressure gas and release it at greater pressure.
Below are some of the most important features and compressor types:
- Positive Displacement in comparison to. Dynamic Compressors:
-
- Positive Displacement Compressors: They work by trapping a certain amount of gas, and then decreasing the volume in order to compress it. The most common types are those that reciprocate (piston-driven) as well as the rotary screw compressor, and Vane-type rotary compressors.
- Dynamic compressors: The compressors function by providing velocity to the gas and then convert that energy into pressure. The most common types are centrifugal compressors and Axial compressors.
- Applications:
-
- Industrial: They are utilized in a variety of industrial processes including pneumatic tools production, petrochemical processing, and power generation. They supply compressed air to devices and processes.
- HVAC and Refrigeration: Compressors play an important part in refrigeration and air conditioning systems. In these, they compress refrigerant gasses to eliminate heat from an area or to cool it.
- oil and Gas: Compressors are crucial in the gas and oil industry to perform processes such as natural gas transmission gas lifting in oil wells as well as gas treatment.
- Food and beverages: Compressors are utilized in the beverage and food sector for tasks such as packaging, bottling, or pneumatic conveyors.
- medical and healthcare: Compressors are located in medical equipment like oxygen concentrators, and respiratory therapy equipment.
- Aerospace Aerospace engines typically include compressors as an element of the propulsion system.
- Types of Positive Displacement Compressors:
-
- Reciprocating Compressor: It uses a piston and arrangement of the cylinder for compressing gas.
- Rotary Screw Compressor: Uses helical screw-like rotating tools to compress gas.
- Rotor Vane Compressor: Uses a rotor that has sliding vanes to compress the gas.
- Types of Dynamic Compressors:
-
- Centrifugal Compressor: Uses a high-speed rotational impeller to transfer energy to the gas that is later converted to pressure as the gas decreases in pressure.
- Axial Compressor: Commonly found within aircraft engines. Axial compressors feature several rows of rotating and stationary blades that compress the gas.
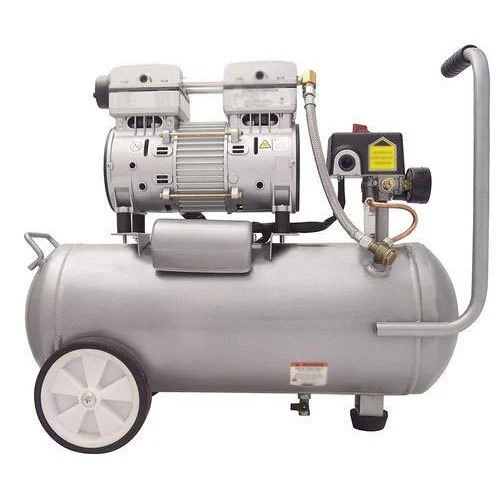
Compressors are chosen according to factors like the pressure ratio required and flow rate, the gases used, as well as demands of the particular application. They are crucial to maintain efficient industrial processes, offering the comfort required in HVAC systems, and permitting a variety of pneumatic and mechanical applications.
Vacuum Pump and Compressor in the comparative chart
Here’s a comparative chart that highlights the key differences between a vacuum pump and a compressor:
Aspect | Vacuum Pump | Compressor |
---|---|---|
Function | Removes air or gases from a sealed container, creating a vacuum (low-pressure environment). | Pressure increases by decreasing volume. |
Purpose | Used for creating a vacuum or low-pressure environment in various applications. | Used for compressing gases or air for a wide range of applications. |
Pressure Range | Operates to reduce pressure below atmospheric pressure (negative pressure). | Operates to increase pressure above atmospheric pressure (positive pressure). |
Types | Various types, including rotary vane, diaphragm, scroll, and turbomolecular pumps. | Various types, including reciprocating, rotary screw, rotary vane, centrifugal, and axial compressors. |
Working Principle | Negative Displacement: Reduces the volume of a gas to create a vacuum. | Positive Displacement (most types): Traps and reduces the volume of gas to increase its pressure. Dynamic (e.g., centrifugal): Imparts kinetic energy to the gas to raise its pressure. |
Applications | Laboratory experiments, vacuum systems, environmental monitoring, medical devices, aerospace simulation, and more. | Industrial processes (pneumatic tools, manufacturing), HVAC and refrigeration, oil and gas, food and beverage, medical equipment, and more. |
Suction Side | Connected to the container being evacuated. | Connected to the source of the gas to be compressed. |
Discharge Side | Discharges to the atmosphere or another container. | Discharges compressed gas for its intended application. |
Pressure Level | Operates at very low pressures, often measured in torr or millibars. | Operates at higher pressures, typically measured in psi or bar. |
Maintenance | Typically requires less maintenance due to fewer moving parts and lower stresses on components. | May require more maintenance due to the wear and tear on moving parts and higher stresses on components. |
Cooling | Often air-cooled, and some types may use oil as a lubricant. | May be air-cooled or water-cooled, and lubrication with oil or synthetic lubricants is common. |
Energy Consumption | Generally consumes less energy compared to compressors. | Consumes energy to compress gases, and energy efficiency varies by type. |
Critical Components | Vacuum chamber, pump mechanism (e.g., vane, diaphragm), and vacuum gauge. | Compression chamber, pistons or rotors (depending on type), valves, and pressure gauges. |
Common Issues | Potential for oil contamination (in oil-sealed pumps), risk of backflow, and sensitivity to leaks. | Potential for overheating, lubrication issues, and wear on moving parts. |
This comparative chart highlights the fundamental differences between vacuum pumps and compressors in terms of their functions, operating principles, applications, and key characteristics. Understanding these distinctions is crucial for selecting the appropriate device for a specific task or process.
Importance of Vacuum Pumps and Compressors
Vacuum compressors and vacuum pumps are essential in a variety of industries and applications. their significance is in the following major areas:
Importance of Vacuum Pumps:
- R&D: Vacuum pumps are crucial for creating controlled lab environments that allow for tests on materials, experiments as well as scientific research in areas like chemistry, physics, and biology.
- Manufacturing Processes: Vacuum pumps are essential to various industries, including semiconductor manufacturing. They remove chambers to ensure accurate and clean processing. This can result in the manufacturing of sophisticated electronic components.
- Manufacturing of pharmaceuticals and food: Vacuum pumps are utilized in the food packaging and pharmaceutical processes. They aid in extending the shelf-life of the products and guarantee safety by eliminating air and sealing the packaging.
- Environmental Monitoring: in environmental sciences, vacuum pumps are utilized to take air samples for the examination of greenhouse gases, as well as other environmental pollutants.
- Health and Medical Devices: Vacuum pumps are essential in medical devices, such as vacuum machines, systems for anesthesia as well as blood-collection systems. They contribute to medical and patient care procedures.
- Aerospace and Space Simulation: Vacuum pumps are used to simulate the atmosphere of space to test satellites, aerospace equipment as well as astronauts’ training.
- Oil and Gas Industry: They are employed to transport natural gas offshore drilling, transmission, and gas processing, which contributes to the transportation and extraction of resources for energy.
Importance of Compressors:
- Production and Industry: Compressors are essential to manufacturing processes, providing power to pneumatic equipment controlling machinery, and making sure that production is efficient.
Tumore prostatico: la prognosi in base a stadio, grado e rischio
class=”wordai-block rewrite-block enable-highlight” data-id=”8″>HVAC and refrigeration: Compressors are essential to cool systems in commercial structures, and refrigeration units that ensure the comfort of customers and the preservation of food items that are perishable.
- Energy Production: Compressors are employed in natural gas power plants, power plant pipelines as well and petrochemical facilities in order to ensure the flow of gases helping to generate energy and distribution.
- Transportation: The use of compressors is in many types of transportation, such as airplanes, automobiles, and trains for purposes like air conditioning braking systems, as well as engine performance.
- Medical and Healthcare Devices: They play a function in medical equipment like oxygen concentrators nebulizers and dental instruments that aid in patient care and treatment.
- Food and Beverage Industry: Compressors are utilized in food processing and packaging to ensure the safety and quality of food products through controlled conditions and sealing processes.
- Environment Control: compressors aid in controlling humidity, air quality, and temperature in data centers, cleanrooms, and controlled areas that are vital to the technology and research sectors.
Vacuum compressors and pumps are essential tools that affect the entire spectrum of applications and industries, providing research, processes, and services that increase the quality of our lives advance our understanding of science, and boost economic growth. Their significance is in their capacity to create a vacuum and boost pressure, which helps in the execution of various vital functions across a variety of industries.
Selection Considerations of Vacuum Pump and Compressor
The selection of the ideal compressor or vacuum pump for a particular application requires looking at a number of factors. Here are a few important considerations for both types of equipment
Considerations for Selecting a Vacuum Pump:
- Applications Requirements: Choose the right vacuum that is required for your particular application. Vacuum pumps of different types can reach different levels of vacuum, ranging from low (e.g. between 1 and 1000 millibars) up to high vacuum (e.g., 0.001 millibars or less). Pick a pump that is able to achieve the desired range of vacuum.
- gas compatibility: Consider the type of gas or vapor that you are dealing with. Certain vacuum pumps are made specifically for certain gases or are not appropriate for certain reactive or corrosive substances. Check that your pump can work with gases that are used in the procedure.
- flow rate: Calculate the necessary flow rate (volume of gas transported per minute) for your particular application. The capacity of the pump must be equal to or over this flow rate in order to ensure effective evacuation.
- Maintaining and reliability: Examine the maintenance requirements that the vacuum pump must meet. Certain pumps require more frequent maintenance while others are designed to provide long-term and trouble-free operation. Take into consideration the availability of spare parts as well as service support.
- Environmental Questions: Evaluate the environmental impacts that the pump has on its environment. For example, sealed pumps with oil can release vapors of oil into the air, and it is possible to choose a dry or oil-free pump for specific applications.
- energy efficiency: Take into consideration the power used by the vacuum pump. The more efficient pump will result in savings over time, particularly for applications that require continuous operation.
- Dimensions and space constraints: Check that the pump will fit in the space that is available and is able to be integrated into your facility or system without any issues.
- Budgeting: Evaluate the initial cost, as well as all costs associated with ownership which includes costs for maintenance and energy for determining the most efficient choice for your needs.
Considerations for Selecting a Compressor:
- Pressure Requirements: Find the outlet pressure that is required for your particular application. Compressors can be found in a variety of pressure ranges. So, choose one that is able to be able to meet or exceed your requirements in terms of pressure.
- The Flow Rate: Determine the flow rates of your compressed air or gas for your specific process. The compressor’s capacity must match or over this flow rate in order to ensure smooth operation.
- Gas Composition: Think about the kind of air or gas you are compressing. Certain compressors are more suitable for specific applications or gases because of compatibility or factors related to the material.
- Continuous vs. Intermittent Operation: Find out whether your project requires a continuous or intermittent compressor. Some compressors are specifically designed for continuous use, while others are more suited to intermittent usage.
- The Oil-Free compressor and. Lubricated: Choose if an oil-free or lubricated compressor is required. The oil-free compressor is typically preferred for applications where contamination with oil is a problem.
- cooling requirements: Consider the cooling technique required by the compressor, regardless of whether it’s water-cooled or air-cooled depending on your specific environment and application.
- Low Noise: Assess the volume of noise amount generated by the compressor in particular if it is going to be installed in a noisy area or near to the workers.
- Space Constraints: Check that the compressor’s dimensions and configuration are within the space that is available in your facility.
- Energie Efficiency: Choose a compressor with high energy efficiency, allowing you to lower the operating cost, specifically when it comes to applications that are used continuously.
- Budgeting: Balance the initial purchase price with the ongoing operating costs and maintenance costs to find the most efficient compressor to meet your requirements.
In both instances, speaking with manufacturers or experts performing performance tests and analyzing the particulars of your particular application are vital actions to make an informed decision. In addition, safety concerns such as pressure relief systems as well as proper ventilation, must be considered in the process of deciding on both compressors and vacuum pumps.
Conclusion
The choice between a pump and compressor is based on the particular needs of the application. Vacuum pumps are perfect for establishing low-pressure environments while compressors can be used to boost air or gas pressure. Be aware of factors like pressure levels and the flow rate, compatibility with gas maintenance requirements, and environmental aspects to make a well-informed choice that fits with your business’s objectives and requirements.